Besides cutting discs, abrasive flap discs are widely used in most blending and finishing applications. So, what is an angle grinder flap disc, and how can you choose a disc that is appropriate for your work?
This article will provide necessary information on this particular disc type, including its uses, guide to choose a disc, and how to use it safely and efficiently.
Contents
What Is An Angle Grinder Flap Disc?
A flap disc consists of many overlapping flaps. Each flap has two sides.
On one side, there are coated abrasive grains (the same grains used in bonded abrasive cutting/grinding discs) to grind or shape surfaces during material fabrication or when bending or polishing a weld.
On the remaining side, there is a backing cloth made of cotton, polyester, or a blend of these two fabrics. This cloth is divided into smaller strips and placed overlapped to add more stability and support to the disc.
A sanding flap disc is more popular than a grinding disc, thanks to its versatility, durability, and lightweight. It can be used for grinding, blending, or finishing a working surface with less noise, less heat, and less vibration.
Despite its higher unit cost, this disc is more cost-effective in the long run since it can be continued to use even when the flaps erode.
Types Of Angle Grinder Flap Disc
There are 3 main types of flap discs – flat discs, conical discs, and compressed-shaped discs. These disc types work at different angles and provide various performance features.
1. Flat discs (or Type 27 discs)
This type has flat grinding surfaces for smooth bending or finishing applications.
This disc type can be used at an angle of 0-15 degrees.
2. Conical discs (or Type 29 discs)
These discs have a depressed center and a maximum contact at the surface, making them excellent for aggressive stock removal or high-volume grinding.
This disc type can be used at an angle of 15-35 degrees.
3. Compressed-shaped discs
These discs have appeared recently on the market as effective on edge grinding, deburring, or heavy weld removal.
The flaps of these discs can grind material in 4 degrees for longer disc life. This disc shape results in a tough edge and high performance.
Angle Grinder Flap Disc Uses
An angle grinder flap disc can work on various materials:
1. Aluminum
Aluminum material can easily melt and cover the grits due to its low melting temperature. Hence, you should apply light and even pressure.
You should also use a T29 conical disc at a 15-degree angle for general grinding purposes or a T27 flat disc for cleaning the surface or making a smooth finish with light and even pressure.
2. Wood
Flap disc can work on wood as well as on metal. For woodworking, you should choose the grit sizes of 120, 150, 180, 220. And always remember to start with coarse grits, then finish your work with lighter grits (100+) to minimize material damages.
3. Paint
You can use flap discs, especially non-woven flap discs with aluminum oxide grains, to remove paint and rust on old furniture and cars.
4. Concrete
Flap discs with silicon carbide and diamond grits are excellent for removing stock on hard materials like concrete without high pressure. Apart from concrete, these discs can also be used on stone, marble, granite, and ceramic.
Guides On Choosing An Angle Grinder Flap Disc
Shapes
Flap discs for angle grinders come with 4 specialty shapes – Trimmable, Aluminum-backed, Mini, and Angled.
- Trimmable: Trimmable flap discs have a trimmable composite backing cloth for added versatility and flexibility and minimum marks to work on hard-to-reach areas like odd-shapes and fillet welds.
- Aluminum-backed: Aluminum-backed discs are supportive of heavy-duty applications like water pipeline fabrication.
- Mini: A mini disc has a diameter of only 2 to 3 inches. This compact size makes them ideal for performing in tight spaces or hard-to-reach areas. These small flap discs can be used as an alternative to blending discs.
- Angled: These flap discs have curved flaps around the blacking plate’s edge, providing easy maneuverability over various grinding angles. You can use these discs for fillet welds, T-joint grinding, or even on flat surfaces.
Sizes
The size of a flap disc is measured by its diameter. A flap disc often has a diameter of between 4 inches and 7 inches.
Discs with smaller diameters rotate faster, making them suitable for fast, smooth grinding in tight spaces. Larger discs can spin slower, but they provide more abrasive and durable for large stock removal.
Width of each flap
Most flap discs on the market have a width of 25mm, while some large-scaled ones have a width of 30mm. Larger flaps are suitable for high-volume, aggressive grinding applications, thanks to their expansive grinding surface.
Flap density
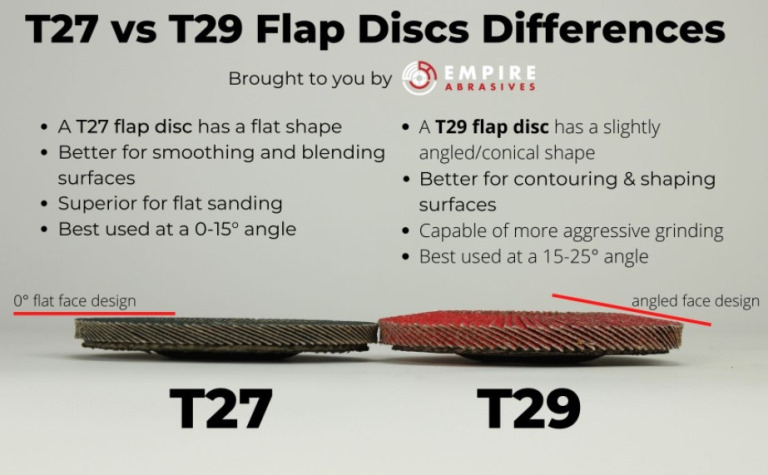
Unlike standard flap discs, high-density flap discs have more abrasive backing cloth for added performance and control. There are 2 flap density levels for a flap disc:
- Type 27: This straight disc density can blend, grind, or finish flat surfaces with an angle of 0-15 degrees.
- Type 29: This angled/conical disc density is often used in aggressive stock removal or smoothing odd-shaped surfaces at an angle of 15-35 degrees.
Grit size
Like sandpaper pads, flap discs come in a wide variety of abrasive grit sizes, ranging from 36 to 120. Smaller grit sizes indicate coarse grit, while larger ones indicate finer grit. For example, a 20 grit flap disc can be used for rust removal on old steel furniture but is not efficient when working on fine polishing.
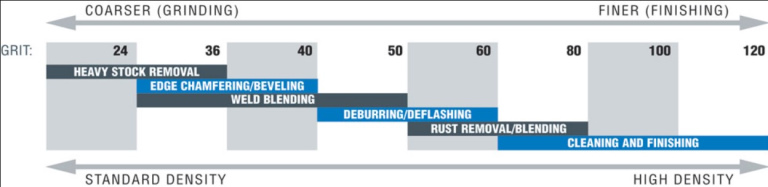
You should generally begin with a coarser grit size to remove stock and shape your workpiece, then use the finer grit size in the finishing step (like blending and repairs). The grit sizes are divided into the following ranges:
- For heavy stock removal: 36 to 40 grits
- For edge beveling and chamfering: 36 to 60 grits
- For weld grinding and blending: 40 to 60 grits
- For deflating and deburring: 60 grits
- For blending and rust removal: 60 to 80 grit
- For delicate applications like finishing and cleaning: 80 to 120 grits
Backing materials
There are 3 backing materials for a sanding flap disc:
- Phenolic: A phenolic backing is lightweight and wear-resistant because it consists of many layers of resin and glass-based fabric. This backing reduces scratches to the working surface.
- Aluminum: A disc with an aluminum backing is best for heavy-duty applications. This backing is sturdy and stable, allowing it to smoothen bevels with no stuck pits. Aluminum backings can also be recycled easily.
- Composite: You can make a small size and shape adjustment on hard-to-reach areas effortlessly with no markings with the help of a composite backing.
Material of flap disc
- Ceramic alumina: This type provides the best performance when working on tool steel, standard steel, armored steel, Inconel, titanium, high-nickel alloys, aluminum, and stainless steel. Besides, this material provides a high, fast cut rate with less generated heat, minor discoloration, and less material loss on heat-sensitive materials.
- Zirconia alumina: A zirconia alumina disc can sharpen itself and maintain its peak performance under high temperatures and hard pressure. Hence, it is ideal for aggressive stock removal and heavy-duty edge grinding, mainly carbon steel, cast iron, stainless steel, and structural steel.
- A mix of ceramic alumina and zirconia alumina: This combination helps you grind with less time, higher precision, and extended disc life. You should use it on carbon steel, structural steel, cast iron, and stainless steel.
- Aluminum oxide: A wheel with aluminum oxide grains is rugged and durable and can deliver consistent grinding on workpieces made of cast iron or steel. Yet, it is not shelf-sharpening, meaning that its crystal grains will dull over time.
How To Use An Angle Grinder Flap Disc?
To use and care for a flap disc properly, you should check the following do’s and don’t.
Things to do
- Do use a flap wheel at its appropriate angle and recommended working surfaces. Otherwise, the flaps and the backing cloth will be damaged quickly. For example, a DeWalt Type 27 flap disc should be used only at an angle of 0-15 degrees.
- Do match the disc’s size with your angle grinder or sander. For example, a 115mm wheel should be used with a 4.5-inch angle grinder.
- Do regularly check for any damage signs on the angle grinder and the flap disc before using it. If the disc has been dropped or mishandled, you should replace it with a new one.
- Do store abrasive flap wheels in their container box at a humidity of 40-50% and a temperature of 60-80oF (15-29oC). Keep them away from water or other fluids.
- Do unplug the angle grinder from its power supply (electricity/battery) before switching discs/attachments.
- Do wear personal safety gear when working with power tools like angle grinders. A safety gear collection includes a full-face shield, eyeglasses, hearing protection, gloves, apron, safety shoes, etc.
Things to avoid
- Don’t use flap discs without the safety guard. The guard on your angle grinder should always be appropriately positioned between you and the disc to prevent unwanted accidents.
- Don’t exceed the rated RPM of a flap wheel.
- Don’t store the discs in direct sunlight, near heat sources, or concrete floors.
- Don’t use loose clothing or accessories that can get stuck onto the moving disc of your angle grinder.
- Don’t use flap wheels or any cutting/grinding discs if you have not adequately trained to use them or not read all safety documentation.
FAQs (Related Questions)
1. Can you cut with a flap disc?
You can cut hard materials like stainless steel, titanium, and cobalt with some type of flap wheels (like a Dark-Fire one). This disc delivers a high cut-rate with great heat sensitivity.
2. What grit flap disc do I need?
You should choose smaller grit sizes in the first step (like shaping and removing stock) and larger grit sizes in the polishing/finishing step.
For example, a Ryobi flap wheel with a grit size of 36 is suitable for heavy stock removal.
3. What is the difference between Type 27 and Type 29 flap discs?
Due to their conical shape, Type 29 flap wheels are often used on aggressive stock removal or reaching irregular shapes. These discs can be used at appropriate angles of 15-35o.
Reversely, Type 27 flap wheels are popularly applied on flat surfaces for smooth grinding, blending, and finishing. These discs can be used at angles of 0-15o.
3. How to attach flap disc to angle grinder?
To attach a flap disc to your angle grinder:
- Correctly install the safety guard;
- Place the lower adapting nut with the raised center facing away from the grinder;
- Install the flap disc with its arbor hole centered over the raised flange and the abrasive flap disc facing away from the grinder;
- Thread the top of the adapting nut onto the spindle. Then place its raised center facing away from the grinder with the same direction as the lower adapting nut;
- Locate, then press and hold the spindle lock. After that, tighten the lock with a spanner wrench;
- When the two adapting nuts have been tightened, the top nut should rest at the center of the backing plate.
Some important notices:
- Never attach the flap disc when your angle grinder is plugged in.
- Always wear protective gloves because the flap discs are made of coarse abrasives
Final Words
Flap wheels are versatile attachments that you should have when working with your angle grinder or sander. When picking up an angle grinder flap disc, you should consider essential factors like its shape, diameter & width, grit size, backing/flap fabric, and flap density.
Besides, you should follow safety cautions and remember to use the wheel that is properly matched with your angle grinder to ensure its performance and safety.